Simulation – Post mortem or part of the design process.
More often than not I receive requests to do a FEA analysis of a design that has failed or is in risk of failure. FEA has for to long been used as an after thought instead of actually part of the design process. This “post mortem” way of approaching simulation is highly inefficient. The time and money spent in the design-analyze-redesign process could be better used. For example, if during the course of the design a part or assembly is at possible risk of failure, those CAD files could be sent out for evaluation while the rest of the design work continues. Since most 3D CAD programs have associative capabilities with their respective 2D drawings, it only makes sense to bring in FEA concurrently.
Where companies that don’t have an analyst on staff, this may seem like an impossibility. But, with better, faster high speed internet connections, it is now worth a serious look.
One last point. FEA simulation doesn’t mean “we don’t have to test it”. There’s an old adage that says, “a single test is worth a thousand expert opinions”. So, think of it this way, simulation will limit the number of tests. 🙂
Thousands of this part were made only to find out it would fail soon after it was in use.
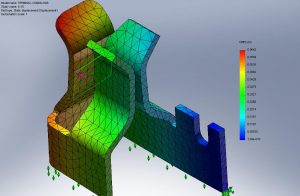